High-End Finite Element Analysis & Simulation Services
TEN TECH LLC provides Subject Matter Expertise in the areas of Structural Dynamics, Fluid and Thermal Analysis & Simulation through the use of advanced numerical techniques such as Finite Element, Finite Difference, Lattice Boltzmann and Boundary Element Methods.
Our core competency is in shock, vibration and electronics cooling analysis of Embedded Defense Electronics systems such as Single Board Computers, RF & Microwave Components as well as complete rugged chassis and subsystems for Avionics, Flight Data Recorders, Guidance & Navigation, Radar Processing, Electronic Warfare and C4ISR applications. A perfect understanding of MIL-STD-810, MIL-S-901, MIL-STD-167, DO-160, AECTP 4000, GR-487 and other environmental specifications, along with decades of experience in the design and analysis of Embedded Systems allows TEN TECH LLC to support the largest and most complicated of programs, being Air, Land, Sea or Space.
Our core competency is in shock, vibration and electronics cooling analysis of Embedded Defense Electronics systems such as Single Board Computers, RF & Microwave Components as well as complete rugged chassis and subsystems for Avionics, Flight Data Recorders, Guidance & Navigation, Radar Processing, Electronic Warfare and C4ISR applications. A perfect understanding of MIL-STD-810, MIL-S-901, MIL-STD-167, DO-160, AECTP 4000, GR-487 and other environmental specifications, along with decades of experience in the design and analysis of Embedded Systems allows TEN TECH LLC to support the largest and most complicated of programs, being Air, Land, Sea or Space.
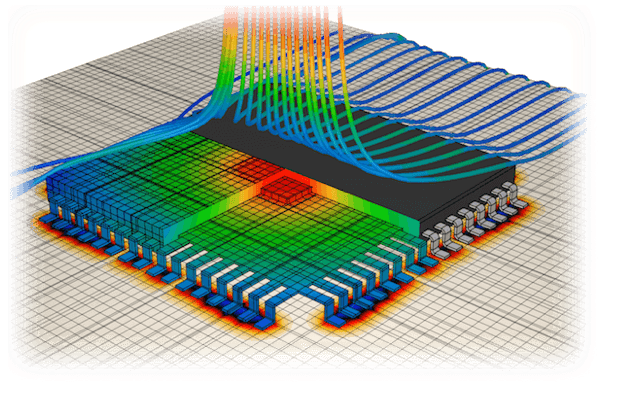
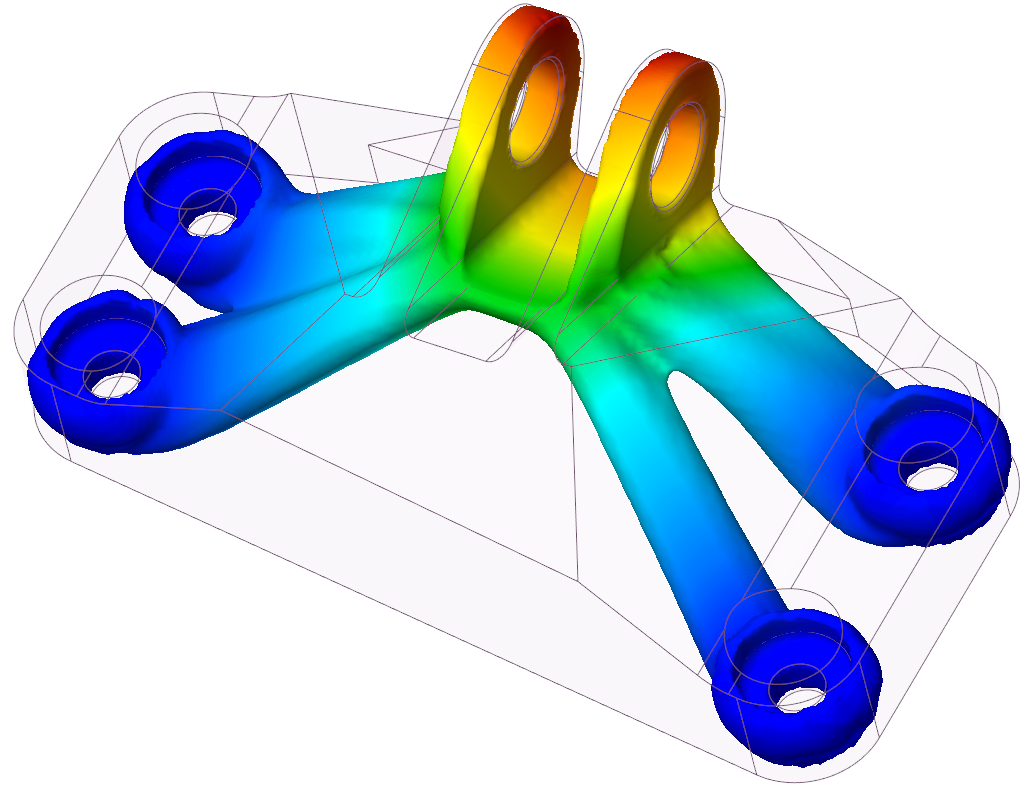
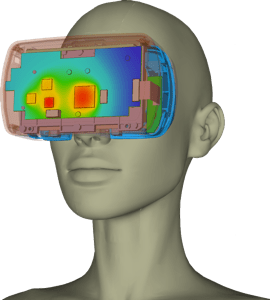
While our roots are heavily set in the Aerospace & Defense industry, our expertise extends to many other industries such as High Tech Electronics, Consumer Products, Automotive & Transportation, Heavy Machinery and Renewable Industry. We understand the issues and challenges engineering and manufacturing companies face every day. Using classic methods and advanced CAE applications, TEN TECH LLC performs the following types of analysis:
- Static and thermo-mechanical Stress
- Quasi-static Acceleration
- Linear & Non-linear Buckling
- Natural Frequencies & Mode Shapes
- Random Vibration, Sine, Sine-on-Random
- Aircraft Windmilling Analysis
- Impact, Drop, Shock, Pyroshock
- UNDEX & DDAM Analysis
- Motion, Kinematics, Rigid & Flexible Body
- Thermal stress, CTE mismatch
- Thermal analysis, orbital heat transfer
- Topology Optimization
- Venting & Decompression Analysis
- High Cycle and Low Cycle Fatigue analysis
- Thermal Cycling & Creep Analysis
- Fracture and Crack Propagation analysis
- Gasket Compression Analysis
- Rapid Dynamics, Crash & Ballistic Impact
- Coupled Thermal-CFD for electronics cooling
- External Aerodynamics & Wind Loads
- Acoustics & Vibro-Acoustics
- Static & Dynamic Aeroelasticity, Flutter
- Electrostatic and Electromagnetic Analysis
- Additive Manufacturing Process Simulation
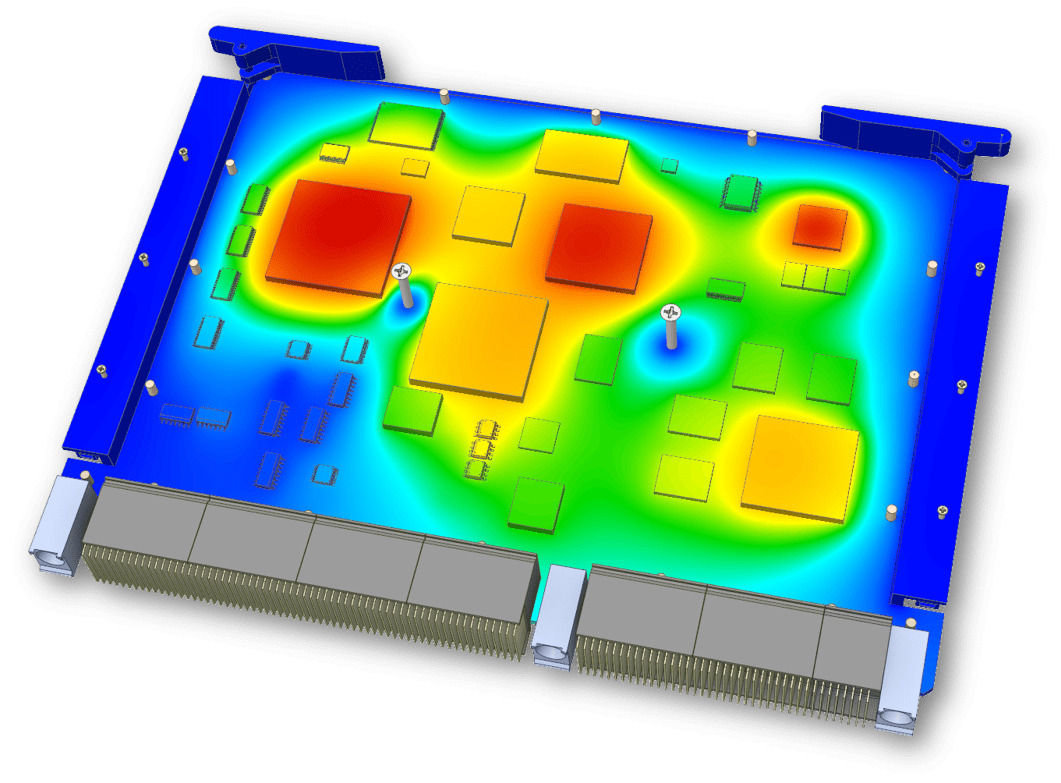
TEN TECH LLC provides expertise in the field of Computational Reliability Analysis, also known as Design for Reliability (DfR), such as:
- System Reliability, including MTBF Prediction, Redundancy Analysis,
- HALT & HASS Test Planning and HALT MTBF Growth Estimates,
- Accelerated Qualification Test Plans
- Design Failure Mode and Effects Analysis (DFMEA)
- Reliability Growth, Environmental Profiling
- Engelmaier BGA Fatigue Life and Parametric Reliability Analysis
- Junction Temperature Modeling, RF Power Efficiency
- Shock & Vibration Accelerated Test Plans, Isolator Design
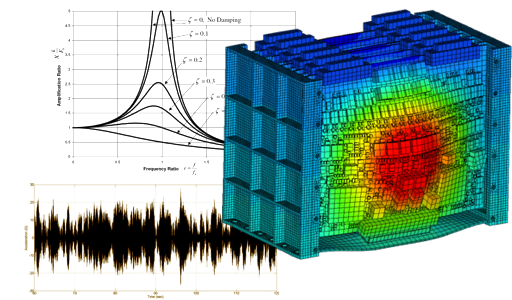
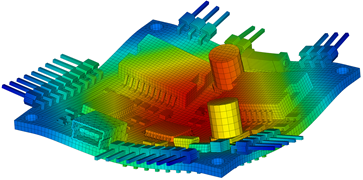
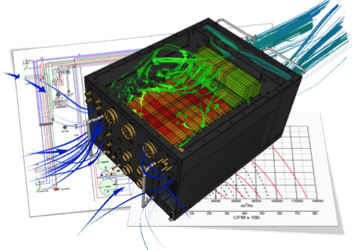
TEN TECH LLC continuously invests in advanced CAE technology, processes, tools and training. Our CAE arsenal comprises most of the high-end software systems available on the market, including ANSYS, Optistruct, Simcenter and more. Combined with our Subject Matter Expertise and our High Performance Computing cluster environment, TEN TECH LLC is able to confidently take on the most challenging multi-physics problems our customers want to solve. Every TEN TECH LLC engineer is well versed in the use of a multitude of CAE applications for modeling, structural, thermal, fluid dynamics, vibro-acoustics analysis, as well as solder joints fatigue and topology optimization.
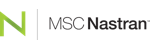
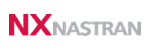
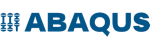
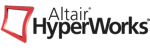
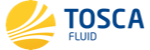
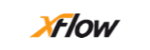
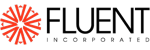
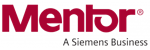
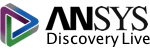
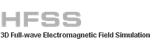
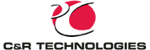
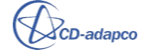
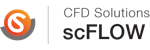
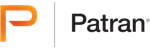
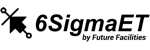
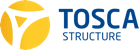
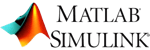
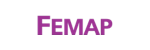
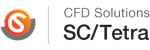
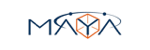
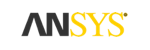
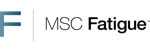
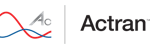
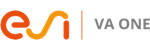
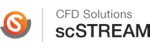
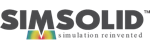
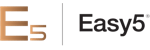
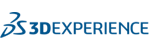
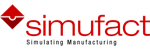
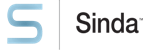
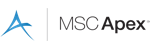
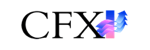
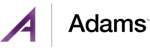
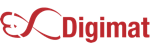
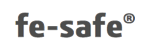
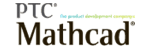
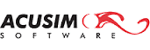
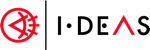
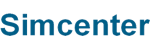
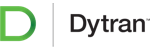
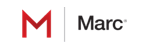
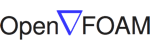
